Mighty Buildings raises $52M to build 3D-printed prefab homes
Mighty Buildings, a startup building tech for prefabricated, ostensibly environmentally-friendly homes, today announced that it raised $52 million in a funding round co-led by Waed Ventures and Bold Capital with participation by Khosla Ventures.
The new tranche, which sources familiar with the matter say values the startup at between $300 million and $350 million, brings Mighty Buildings’ total raised to $150 million. CEO Scott Gebicke says that it’ll be put toward Mighty Buildings’ expansion in North America and the Middle East, particularly Saudi Arabia, and supporting the launch of the company’s next-gen modular homebuilding kit.
“The pandemic aggravated the housing shortage in the US and other countries, as projects needed to be paused and construction workers permanently left the industry,” Gebicke told TechCrunch in an email interview. “Recent interest rate increases, which were expected to cool housing demand, have had the opposite effect, as the secondary market for used houses plummeted, driving ever more demand for newly built homes.”
Mighty Buildings was founded in 2017 by Slava Solonitsyn, Dmitry Starodubtsev, Sam Ruben and Alexey Dubov, who sought to create a platform leveraging 3D printing to help automate the construction industry, specifically the home construction industry. Gebicke, a former naval officer and previously a project lead in McKinsey’s industrial practice, was appointed CEO last December.
3D-printed, prefab homes may sound out of the ordinary. But they’ve become more common as fluctuating construction materials and labor costs push property developers to seek affordable alternatives to traditional home building.
The U.S. is short 650,000 construction workers, according to the trade association Associated Builders and Contractors. And 82.5% of materials — including electrical conduit, steel and concrete — have experienced “significant” cost increases since 2020, per a report in Oxford Economics.
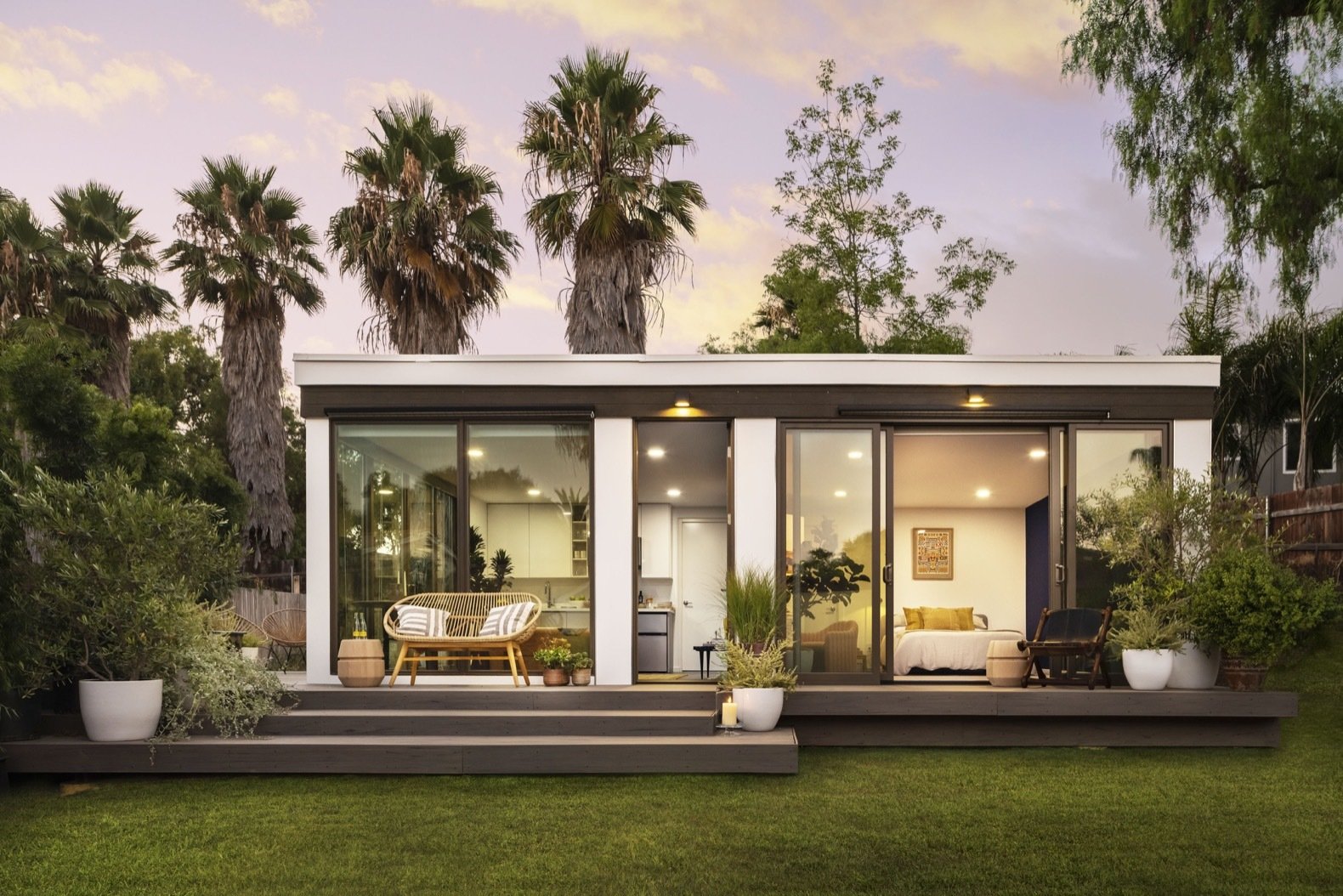
A 3D-printed prefab home by Mighty Buildings.
3D-printed homes promise to be comparatively cheap — and easy to assemble. A 2018 study in the academic journal IOP Science: Materials Science and Engineerings argues that 3D printing can cut costs by at least 35%. And according to industry experts, it takes as little as a month to piece together an entire 3D-printed home — far shorter a time frame than the six to eight months spent constructing a typical house.
Charitable organizations including Habitat for Humanity have begun to print homes for families, and neighborhoods of 3D-printed homes — albeit quite small ones — have begun to spring up.
“We typically compete against traditional building methodologies, such as stick-built single family homes in the U.S. and concrete precast in the Middle East,” Gebicke said. “In most developed and developing nations in the world, the industry must build more homes much faster in order to address the supply shortages.”
Mighty Buildings provides a prefabricated kit of parts to developers, who use its product to build residential structures. Initially, San Francisco-based Mighty Buildings sold prefab homes directly to customers. But within the past two years, the startup has shifted to selling whole communities of homes to developers.
The company claims its proprietary printed material, made of 60% recycled glass, is five times the strength of concrete, 70% the weight and produces fewer carbon emissions during manufacturing. It’s also rated for winds up to 150 miles per hour — hurricane-force, in other words — and compliant with the California Building Code, including Title 24 Energy requirements and other regulatory standards.
Mighty Buildings employs ultraviolet light to cure its material off-site. This allows for “highly refined” and “unique” shapes with a range of customization options, the startup says, while reducing waste as only the material that’s required is cured.
“Our factory-based advanced manufacturing techniques deliver automotive grade quality control,” Gebicke said. “Moreover, our microfactories can be commissioned rapidly with relatively low capital expenditure, enabling production at scale.”

Image Credits: Mighty Buildings
Of course, Mighty Buildings’ prefab homes aren’t for everyone. Given the newness of the tech, few home professionals — think electricians, plumbers and so on — are likely to be familiar with the nuances of a 3D-printed home in the event something goes wrong. And while platforms like Mighty Buildings’ allow for some customization, the printing-based manufacturing process limits the homes to certain designs.
But as the housing shortage grows, so does the 3D-printed construction market. Straits Research estimates that it’ll be worth $47.95 billion in 2030.
Mighty Buildings is seeing its own customer base tick up, with revenue reaching around $5 million in 2022, according to Gebicke. He claims that the startup has a pipeline of projects in the U.S., Caribbean and Middle East that could be worth in “hundreds of millions” within the next few years.
The competition’s stiff. Mighty Buildings competes with a number of players in the burgeoning 3D-printed construction sector, including Icon, Peri 3D, CyBe, Alquist 3D, Printed Farms and Nidus 3D. But Gebicke asserts that Mighty Buildings is making moves from a position of strength.
“We’re now working with some of the largest developers in the U.S. and in the Middle East to build very large numbers of homes very quickly and scalably in order to address the global housing shortage,” Gebicke added.